What are the Different Types of Forging Processes?
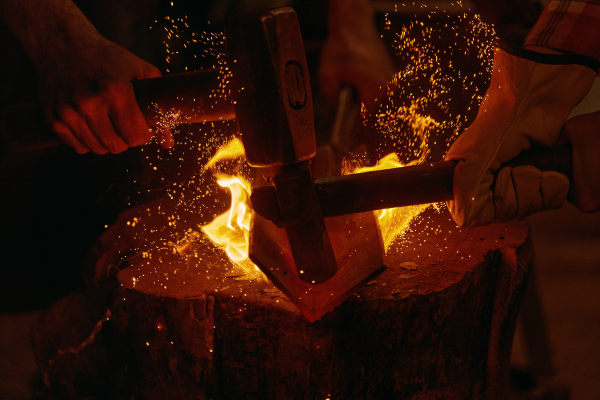
Four types of forging manufacturing processes are commonly used to shape metal parts. These metal forging processes include impression die forging (closed die), open die forging, cold forging, and seamless rolled ring forging. Using localized compressive forces, metal forgings provide a highly effective way to create various parts for all applications.
Great Lakes Forge is a proud provider of open die forging services and other types of forging operations. Contact us today for more information about open die forging and learn what we can do for you.
Impression Die Forging
Often referred to as closed die forging, the impression die forging process utilizes dies that completely enclose the base material, making it easier to shape the material into its desired shape. Compared to other types of forging operations, impression die forging requires greater compressive forces to ensure the die cavities are filled and form the complete part.
Impression Die Forging Advantages
- Generate less metal waste
- Higher production rates
- Provides enhanced fatigue and impact resistance
- Produces parts with higher strength-to-weight ratios
Cold Forging
The cold forging process is designed to create parts and components that display enhanced surface finish quality and tight tolerance dimensions. Unlike most other types of forging, cold forging does not utilize heat for part structure shaping but rather colder temperatures to produce various components.
Cold forging is used to create various parts and components, including shafts, hollow parts with shafts and stems, odd configurations, and cup-shaped geometries.
Cold Forging Advantages
- Creates tight tolerances
- Produces good surface finish quality
- Economical
- Little to no material waste
- Dies last longer than those used for heat forging
- Increased yield and tensile strength
- Gold
- Silver
- Copper
- Brass
Cold Forging Material Options
- Gold
- Silver
- Copper
- Brass
Open Die Forging
Also referred to as hammersmith forging, open die manufactured parts are shaped through direct force. A hammer strikes and deforms the workpiece, held in place by two flat dies. This process is called open die forging because the dies do not enclose the workpiece. Within this metal forging process, the dies act more like tools rather than enclosed molds.
Open die forging can produce forgings from a few pounds up to more than 150 tons and is ideal for parts weighing over 200,000 lbs. and 80 feet long.
Open Die Forging Advantages
- Improved fatigue resistance
- Continuous grain flow
- Longer part life
- Increased strength
- Less chance of voids
- Finer grain size
Seamless Rolled Ring Forging
Typically performed by punching a hole in a thick, round piece of metal and then rolling and squeezing the donut into a thin ring, seamless rolled ring forging processes are ideal for producing ring diameters ranging from a few inches to 30 feet. Compared to other types of forging, rolled ring forging utilizes curved dies instead of flat dies to form ring-shaped components.
Seamless Rolled Ring Forging Advantages
- Superior structural integrity
- Increased strength
- Controlled directional flow
- Eliminates welding, inclusions, and porosity
Get the Open-Die Forgings You Need With GL Forge
At Great Lakes Forge, we specialize in forging custom metal components and parts. Our open-die forging process produces high-strength forgings for industries that demand maximum reliability. We work closely with our customers to make sure we forge parts that meet each application’s exact requirements. With secondary services like CNC machining and heat treatment, we can produce blocks, spindles, crankshafts, and other custom-forged components that meet your specifications. From material selection to the final product, you can count on GL Forge for superior quality every step of the way.
Contact Great Lakes Forge for Expert Open Die Forging Services
Great Lakes Forge is your trusted provider of open die forging services for metal part manufacturing. Contact us for more information on our custom forging service options, or call us at 800-748-0217, and we’ll help you find the best custom forging solutions for your project.
Start Your Quote